机床加工过程中扎刀(机械加工扎刀)
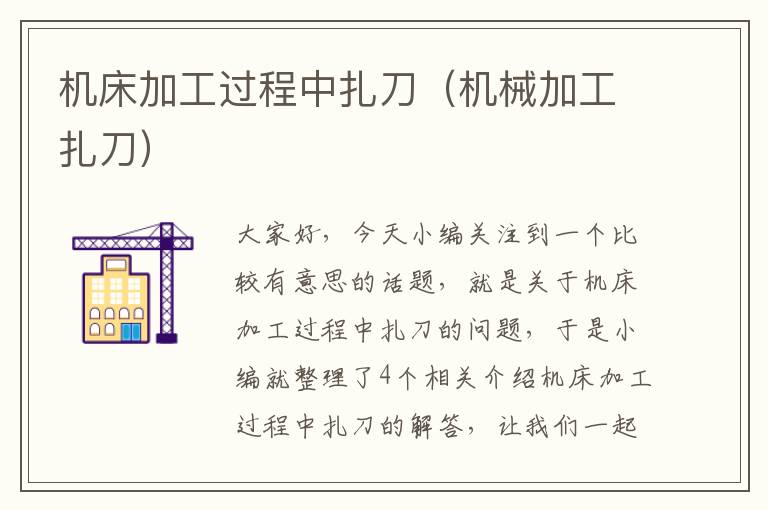
大家好,今天小编关注到一个比较有意思的话题,就是关于机床加工过程中扎刀的问题,于是小编就整理了4个相关介绍机床加工过程中扎刀的解答,让我们一起看看吧。
1、在车床加工时为什么会出现扎刀现象
扎刀的主要原因:(1)车刀的前角太大,机床丝杆间隙较大;(2)车刀安装得过高或过低;(3)工件装夹不牢;(4)车刀磨损过大;(5)切削用量太大;(6)切削油性能不达标。
进行对刀后,没有修正起刀点或错点成定义起刀点,导致扎刀。
产生扎刀的原因主要有:1)刀杆强度低或伸出过长,刚性不足时造成扎刀。为此,在车削外螺纹时最好采用弹簧刀杆以减小振动;车削内螺纹时,应选用较好的刀杆材料或棱形截面刀杆,来增强刚性。
操作不当,退刀不熟练,刀撞击未加工处扎刀。5,车削螺纹时工件装夹不牢,操作不当,拖板各部松动,车第一条螺旋槽与第二次不吻合乱扣扎刀。
车削材料较软而进刀量太大或者刀口太锋利都容易产生扎刀现象 ,解决的办法是选用合适的刀具,刃磨刀口的刃倾角大一些。
2、车削加工扎刀都有哪些原因?
扎刀的主要原因:(1)车刀的前角太大,机床丝杆间隙较大;(2)车刀安装得过高或过低;(3)工件装夹不牢;(4)车刀磨损过大;(5)切削用量太大;(6)切削油性能不达标。
原因:1,刀口不快;2,托板间隙过大;3,机床主轴油间隙;4,刀具强度不够。车床是主要用车刀对旋转的工件进行车削加工的机床。在车床上还可用钻头、扩孔钻、铰刀、丝锥、板牙和滚花工具等进行相应的加工。
产生扎刀的原因主要有:1)刀杆强度低或伸出过长,刚性不足时造成扎刀。为此,在车削外螺纹时最好采用弹簧刀杆以减小振动;车削内螺纹时,应选用较好的刀杆材料或棱形截面刀杆,来增强刚性。
对刀位Z向数值过大,当刀具伸出长度较长时,进行对刀,刀具直接扎到对刀仪上。5)加工一段后,发现Z向起刀点错误,调整后,没有结束加工(ALT S)就继续加工导致扎刀。
3、插补加工时有扎刀现象
缺乏充足润滑:在金属和硬质材料的加工过程中,使用过少的液体冷却剂或润滑油,也容易导致高温和切削力集中,进而引起扎刀。加工场地不稳定:如设备放置不平或周围环境嘈杂,也会对加工精度造成干扰,引发扎刀问题。
原因:1,刀口不快;2,托板间隙过大;3,机床主轴油间隙;4,刀具强度不够。车床是主要用车刀对旋转的工件进行车削加工的机床。在车床上还可用钻头、扩孔钻、铰刀、丝锥、板牙和滚花工具等进行相应的加工。
进给太大,刀具磨损,排削槽过小,吃刀量太大,丝杠等机床精度不稳定(一般不能)没根据材料的性能选者好合理的刀具,切削速度,进给量,刀具角度等等。(比如A3钢材 普通时候黏度很高(塑性)。
车刀磨损过大:引起切削力增大顶弯工件出现扎刀,此时应对车刀加以修磨。(5)切削用量(主要是背吃刀量和切削速度)太大:根据工件导程大小和工件刚性选择合理的切削用量。
4、数控车床对刀时扎刀什么原因?
原因:1,刀口不快;2,托板间隙过大;3,机床主轴油间隙;4,刀具强度不够。车床是主要用车刀对旋转的工件进行车削加工的机床。在车床上还可用钻头、扩孔钻、铰刀、丝锥、板牙和滚花工具等进行相应的加工。
车刀磨损过大:引起切削力增大顶弯工件出现扎刀,此时应对车刀加以修磨。(5)切削用量(主要是背吃刀量和切削速度)太大:根据工件导程大小和工件刚性选择合理的切削用量。
下面简单介绍下车削螺纹时常见故障及解决方法:扎刀主要原因:(1)车刀的前角太大,机床丝杆间隙较大;(2)车刀安装得过高或过低;(3)工件装夹不牢;(4)车刀磨损过大;(5)切削用量太大。
工件装夹不牢:工件本身的刚性不能承受车削时的切削力,因而产生过大的挠度,改变了车刀与工件的中心高度,形成切削深度突增出现扎刀,此时应把工件装夹牢固,可使用尾座顶尖等,以增加工件刚性。
到此,以上就是小编对于机床加工过程中扎刀的问题就介绍到这了,希望介绍关于机床加工过程中扎刀的4点解答对大家有用。
[免责声明]本文来源于网络,不代表本站立场,如转载内容涉及版权等问题,请联系邮箱:3801085100#qq.com,#换成@即可,我们会予以删除相关文章,保证您的权利。 转载请注明出处:/jiagong/44324.html