机床主轴间隙故障分析图(机床主轴间隙故障分析图片)
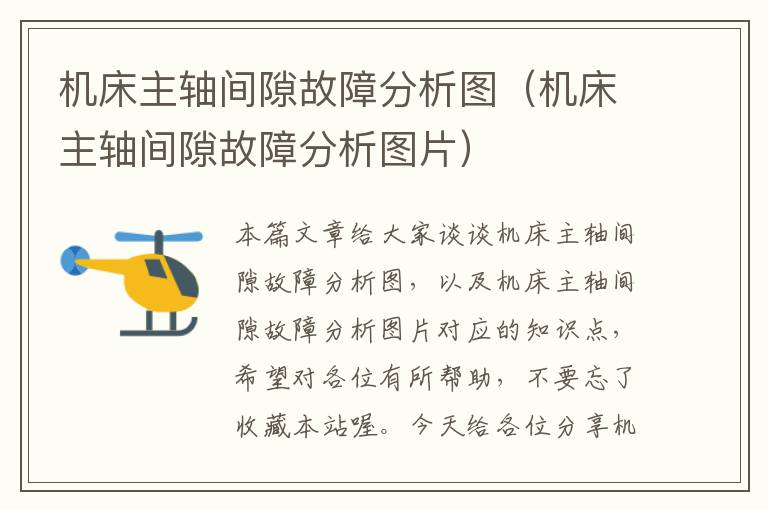
本篇文章给大家谈谈机床主轴间隙故障分析图,以及机床主轴间隙故障分析图片对应的知识点,希望对各位有所帮助,不要忘了收藏本站喔。 今天给各位分享机床主轴间隙故障分析图的知识,其中也会对机床主轴间隙故障分析图片进行解释,如果能碰巧解决你现在面临的问题,别忘了关注本站,现在开始吧!
1、6140车床主轴间隙如何调整?
当间隙产生时,首先松开轴承螺母的紧定螺钉,转动间隙调整螺母,使带有锥度的滚动轴承内圈沿轴向移动,消除间隙。然后进行试转,当主轴在最高转速下不发生过热,用手转动无阻滞感,然后拧紧紧定螺钉就可以了。
主轴轴承应在无间隙(或少量过盈)的条件下进行运转,因此,主轴组件应在结构上保证能调整轴承间隙。CA6140型卧式车床主轴前、后端各有一个螺母,就是用来调整间隙的。
那儿产的?有的主轴轴承是锥度的,有的是轴套。
调整时要根据主轴的跳动对它的间隙调整,间隙过小主轴会发热的,但是热度不超60度就可以,过热要烧轴承的。调整是靠轴承后边的背帽松或紧来达到要求的,不同的主轴它的轴承用的是不一样的调整的方法也不一样的。
2、加工中心主轴维修及常见故障分析
电主轴常见故障的维修分析与排除方法:主轴发热(1)主轴轴承预紧力过大,造成主轴回转时摩擦过大,引起主轴温度急剧升高。故障排除方法:可以通过重新调整主轴轴承预紧力加以排除。
皮带式主轴以高扭力之齿型皮带传动,不打滑,并可大幅度减低加工中心传动噪音及热量产生。电主轴常见故障的维修分析与排除方法:电主轴发热(1)主轴轴承预紧力过大,造成主轴回转时摩擦过大,引起主轴温度急剧升高。
主轴部件动平衡不良,使主轴回转时振动过大,引起工作噪声。故障排除方法:需要机床生产厂家的专业人员对所有主轴部件重新进行动平衡检查与调试。(2)主轴传动齿轮磨损,使齿轮啮合间隙过大,主轴回转时冲击振动过大,引起工作噪声。
主轴轴承润滑油脂耗尽或润滑油脂过多,也会造成主轴回转时阻力、摩擦过大,引起主轴温度升高。故障排除方法:通过重新涂抹润滑脂加以排除。
电主轴常见故障的维修分析与排除方法:主轴发热(1)主轴轴承预紧力过大,造成主轴回转时摩擦过大,引起主轴温度急剧升高。故障排除方法:可以通过重新调整主轴轴承预紧力加以排除。
3、发那科数控车床加工过程中轴有间歇现象?
这是典型的“共振”现象。加工件质量一定,到某转速即可发生共振;或,某转速下工件质量到达某数值时也可产生共振。原因:转速与加工件的综合主频与车床的自振频率发生了谐振。
如在移动中出现该现象态应该是Z轴丝杆上有异物(切削屑或砂粒等)或Z轴丝杆有破裂损伤导致移动到固定部位时小拖板(X轴)会有抖动。如是Z轴移动后动出现则是X轴在间隙补偿。
看看程序模态代码是G61还是G64,G64会自动圆滑过度,G61会准确定位,加工拐角更精准,但是会在程序段之间出现小停顿。这是程序设计的问题,点群插补不要参杂太多M、S、T指令,速度转速不要重复指定,点群只写坐标就好了。
等反向间隙消除后刀具才运动,但是这时数控机床的坐标已经变化了一个值,也就是说坐标值与刀具实际位置已经产生了偏差。如果反复对刀仍然存在较大的尺寸偏差,那么就有可能是参数问题或者是反向间隙过大的问题。
机床刚度不足:机床刚度不足会导致Z轴在加工中发生变形,从而导致加工精度下降、坐标偏移等问题。需要检查机床的结构和零部件是否正常,如滑轨、丝杆等是否有磨损或损坏。
4、数控车床主轴的两个轴承有间隙该怎么调整
当间隙产生时,首先松开轴承螺母的紧定螺钉,转动间隙调整螺母,使带有锥度的滚动轴承内圈沿轴向移动,消除间隙。然后进行试转,当主轴在最高转速下不发生过热,用手转动无阻滞感,然后拧紧紧定螺钉就可以了。
常用调整径向轴承间隙的方法如下:对圆筒形和椭圆形轴瓦的侧隙,可采用手工研刮或轴承中分面加垫车削后修刮的方法调整。对圆筒形和椭圆形轴瓦的顶隙,可采用手工研刮或情况允许时对轴承中分面加垫的方法调整。
前轴承采用内锥孔设计,先松后轴承螺母,再松前轴承左侧螺母 ,再紧右侧螺母,轴承间隙就变小。调整完后,将后轴承间隙调整就行。调整轴承需要技术,调紧了轴承发热要死,调松了振动 较大精度无法保证。看你水平了。
主轴轴承应在无间隙(或少量过盈)的条件下进行运转,因此,主轴组件应在结构上保证能调整轴承间隙。CA6140型卧式车床主轴前、后端各有一个螺母,就是用来调整间隙的。
关于机床主轴间隙故障分析图和机床主轴间隙故障分析图片的介绍到此就结束了,不知道你从中找到你需要的信息了吗 ?如果你还想了解更多这方面的信息,记得收藏关注本站。 机床主轴间隙故障分析图的介绍就聊到这里吧,感谢你花时间阅读本站内容,更多关于机床主轴间隙故障分析图片、机床主轴间隙故障分析图的信息别忘了在本站进行查找喔。
[免责声明]本文来源于网络,不代表本站立场,如转载内容涉及版权等问题,请联系邮箱:3801085100#qq.com,#换成@即可,我们会予以删除相关文章,保证您的权利。 转载请注明出处:/peijian/zhuzhou/43234.html