数控机床主轴孔镗大了怎么补救(镗床主轴锥孔尺寸)
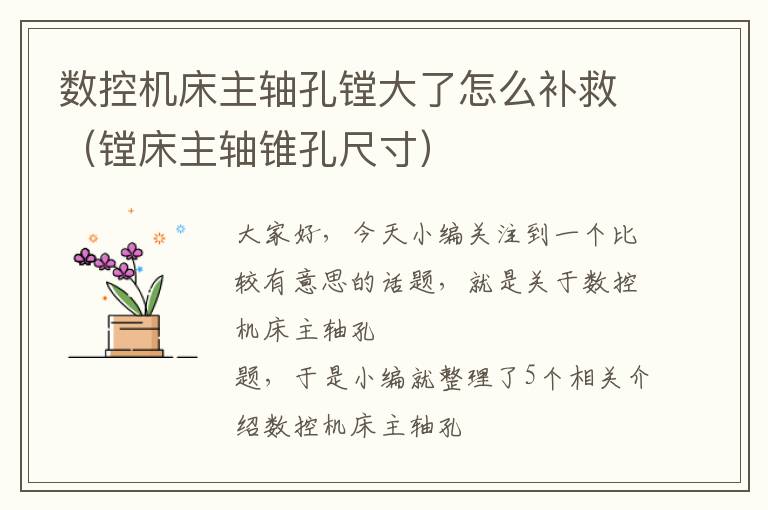
大家好,今天小编关注到一个比较有意思的话题,就是关于数控机床主轴孔镗大了怎么补救的问题,于是小编就整理了5个相关介绍数控机床主轴孔镗大了怎么补救的解答,让我们一起看看吧。
1、轴承孔镗大了怎么补救?
丝。可在内孔处均匀的点焊若干点,然后再加工至尺寸,件不是太大,可送外镀铬处理,轴承内径车大了就使用10丝冷处理来进行补救。 轴承孔是轴承的内孔。
补救镗孔镗大的方法:可以在孔内进行刷镀,可以镀硬铬,如果对孔尺寸要求高,镀后需要对孔进行二次加工,镗或磨内孔。
可以用铸铁焊条在磨损的孔内堆焊一层,然后上镗床把孔重新镗出来。注意两点:一是在堆焊时不可操之过急,注意电流、温度不可太高,防止箱体热变形。二是考虑好箱体在镗床上正确的找正定位的工艺问题,防止镗偏孔。
作为加工件工序来说肯定是废了,因为轴承支撑的面接触变成了线接触,即使轴承装上了很快也会松脱。但如果是大型制件不报废不起,则可以用填焊再加工或镶套方式翻修补救。
2、数控车床镗孔时镗出来的孔偏大和偏小的原因各是什么?
有以下几种可能的原因,请逐一排除:铁屑排出不顺畅。机床X向间隙大,镗孔时未消除间隙。
第一:孔小的时候,铁屑出不来,导致孔的锥度比较大。解决:这个只能靠试程序的时候,边试边改程序。第二:机床水平不好,导致机床锥度。解决:这是机床误差,如果懒得重新调试机床,就凭经验,修改程序。
如果是连续镗孔,没有发生换刀动作,那只能是刀具的原因,1。
可能的原因如下:机床热胀冷缩造成的。毛坯余量不一致造成的。有的零件余量大,有的余量小。数控车床间隙和加工中的让刀作用,综合影响的结果。刀具不锋利,切深太大。
温度,车床加工孔,一般会是镗孔,排除掉安装,刀具等原因,最容易出现问题的是温度控制。刀具出现问题震颤最容易产生的是孔径变小或产生毛刺表面粗糙度变大而造成孔径尺寸变小,而非变大。
3、试述数控车床镗孔时产生误差的原因及修正措施。
加工原理误差加工原理误差是由于采用了近似的加工运动方式或者近似的刀具轮廓而产生的误差,因在加工原理上存在误差,故称加工原理误差。只要原理误差在允许范围内,这种加工方式仍是可行的。
伺服电机轴与丝杠之间的连接松动,致使丝杠与电机不同步,出现尺寸误差。滚珠丝杠与螺母之间润滑不良,使工作台(或刀架)运动阻力增加,无法完全准确执行移动指令。
数控机床机械原因分析:伺服电机轴与丝杠之间的连接松动,致使丝杠预电机不同步,出现尺寸误差。检测时只需在伺服电机与丝杠的联轴节上作好记号。
空大,主要原因有:工件摆头,定位有问题;刀具进给与吃刀量配合出现问题;细长轴,轴颈与长度比例不合适;如果是精加工镗孔的公差大小取决于你的吃刀量大小。
影响数控车床加工精度的因素和改进措施:工艺系统中的各组成部分,包括机床、刀具、夹具的制造误差、安装误差、使用中的磨损都直接影响工件的加工精度。
4、工件镗孔镗大了怎么调试镗刀
因为镗刀刃一定要与主轴轴线对称,如果不对称,会使镗的孔扩大。又因粗镗切削力较大,会是调节螺母产生间隙,产生误差,但不会太大,0.01左右正常,所以可以不要太看重刻度调的完全一致。
大多数镗刀都需要通过试切-测量(cut-and-measure)操作来确定其设定尺寸,即首先对一小部分被加工孔进行试切镗削,然后测量其加工孔径。
解决:这是机床误差,如果懒得重新调试机床,就凭经验,修改程序。第三:镗刀露出过长,到孔有震纹,从而导致孔的锥度。
数控铣床镗刀调内直径260mm的步骤如下:需要确定所使用的刀具是否适合加工内直径为260mm的零件。如果刀具的直径太小,则无法加工出所需尺寸。如果刀具的直径太大,则可能造成切削质量不佳或加工不良。
5、数控上精加工的内孔镗超差后能用啥办法补救?
补救镗孔镗大的方法:可以在孔内进行刷镀,可以镀硬铬,如果对孔尺寸要求高,镀后需要对孔进行二次加工,镗或磨内孔。
扩孔法补救。对于孔椭圆、孔不同心斜孔这一类的孔超差称奇异孔。处理时,在孔的正确位置上,将孔扩大至一定精度,再加工。铍铜内孔超差2丝用扩孔法补救。因为镗孔需要给出一定的镗孔余量,故需要扩孔。
大了几丝不怎么好焊,如果要求不高,可在内孔处均匀的点焊若干点,然后再加工至尺寸。 如果零件不是太大,可送外镀铬处理。 如果不是安装轴承的孔,可将与该孔装配的零件外径加大。
粗镗后应将夹紧压板松一下,再重新进行夹紧,以减少夹紧变形对加工精度的影响。通常精镗背吃刀量大于等于0.01 mm,进给量大于等于0.05 mm/r。
关于数控机床主轴孔镗大了怎么补救和镗床主轴锥孔尺寸的介绍到此就结束了,不知道你从中找到你需要的信息了吗 ?如果你还想了解更多这方面的信息,记得收藏关注本站。 数控机床主轴孔镗大了怎么补救的介绍就聊到这里吧,感谢你花时间阅读本站内容,更多关于镗床主轴锥孔尺寸、数控机床主轴孔镗大了怎么补救的信息别忘了在本站进行查找喔。
[免责声明]本文来源于网络,不代表本站立场,如转载内容涉及版权等问题,请联系邮箱:3801085100#qq.com,#换成@即可,我们会予以删除相关文章,保证您的权利。 转载请注明出处:/peijian/zhuzhou/35646.html