机床加工工件尺寸偏小,车床加工外径尺寸变化大原因
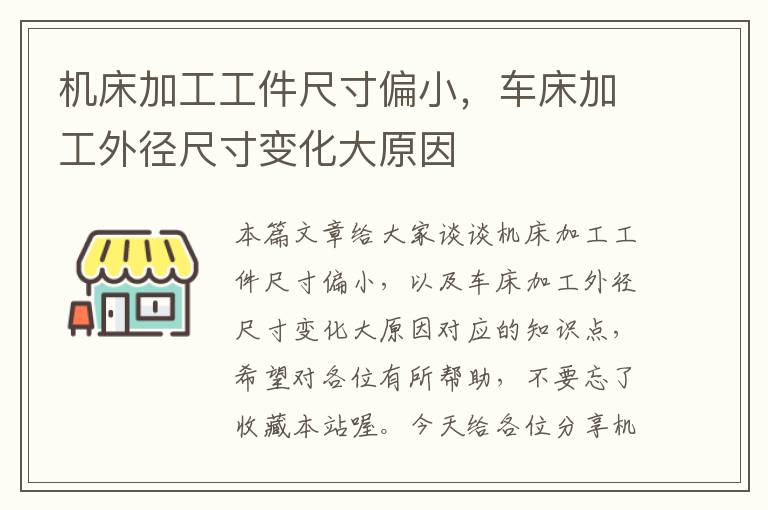
本篇文章给大家谈谈机床加工工件尺寸偏小,以及车床加工外径尺寸变化大原因对应的知识点,希望对各位有所帮助,不要忘了收藏本站喔。 今天给各位分享机床加工工件尺寸偏小的知识,其中也会对车床加工外径尺寸变化大原因进行解释,如果能碰巧解决你现在面临的问题,别忘了关注本站,现在开始吧!
1、CNC加工时发现工件尺寸不精确?
1)修改刀补值保证尺寸精度由于第一次对刀误差或者其他原因造成工件误差超出工件公差,不能满足加工要求时,可通过修改刀补使工件达到要求尺寸,保证径向尺寸方法如下:
a. 绝对坐标输入法根据“大减小,小加大”的原则,在刀补001~004处修改。
如用2号切断刀切槽时工件尺寸大了0.1mm,而002处刀补显示是X3.8,则可输入X3.7,减少2号刀补。
b. 相对坐标法如上例,002刀补处输入U-0.1,亦可收到同样的效果。
同理,对于轴向尺寸的控制亦如此类推。
如用1号外圆刀加工某处轴段,尺寸长了0.1mm,可在001刀补处输入W0.1。
2)半精加工消除丝杆间隙影响保证尺寸精度对于大部分数控车床来说,使用较长时间后,由于丝杆间隙的影响,加工出的工件尺寸经常出现不稳定的现象。
这时,我们可在粗加工之后,进行一次半精加工消除丝杆间隙的影响。
如用1号刀G71粗加工外圆之后,可在001刀补处输入U0.3,调用G70精车一次,停车测量后,再在001刀补处输入U-0.3,再次调用G70精车一次。
经过此番半精车,消除了丝杆间隙的影响,保证了尺寸精度的稳定 数控,机床,模具设计,数控车床,数控技术3)程序编制保证尺寸精度a. 绝对编程保证尺寸精度编程有绝对编程和相对编程。
相对编程是指在加工轮廓曲线上,各线段的终点位置以该线段起点为坐标原点而确定的坐标系。
也就是说,相对编程的坐标原点经常在变换,连续位移时必然产生累积误差,绝对编程是在加工的全过程中,均有相对统一的基准点,即坐标原点,故累积误差较相对编程小。数控车削工件时,工件径向尺寸的精度一般比轴向尺寸精度高,故在编写程序时,径向尺寸最好采用绝对编程,考虑到加工及编写程序的方便,轴向尺寸常采用相对编程,但对于重要的轴向尺寸,最好采用绝对编程。b. 数值换算保证尺寸精度很多情况下,图样上的尺寸基准与编程所需的尺寸基准不一致,故应先将图样上的基准尺寸换算为编程坐标系中的尺寸。
如图2b中,除尺寸13.06mm外,其余均属直接按图2a标注尺寸经换算后而得到的编程尺寸。
其中,φ29.95mm、φ16mm及60.07mm三个尺寸为分别取两极限尺寸平均值后得到的编程尺寸。
4)修改程序和刀补控制尺寸数控加工中,我们经常碰到这样一种现象:程序自动运行后,停车测量,发现工件尺寸达不到要求,尺寸变化无规律。
如用1号外圆刀加工图3所示工件,经粗加工和半精加工后停车测量,各轴段径向尺寸如下:φ30.06mm、φ23.03mm及φ16.02mm。
对此,笔者采用修改程序和刀补的方法进行补救,方法如下:
a. 修改程序原程序中的X30不变,X23改为X23.03,X16改为X16.04,这样一来,各轴段均有超出名义尺寸的统一公差0.06mm;b. 改刀补在1号刀刀补001处输入U-0.06。经过上述程序和刀补双管齐下的修改后,再调用精车程序,工件尺寸一般都能得到有效的保证。数控车削加工是基于数控程序的自动化加工方式,实际加工中,操作者只有具备较强的程序指令运用能力和丰富的实践技能,方能编制出高质量的加工程序,加工出高质量的工件。
调整加工精度尺寸有很多方法的。
1.如你是手工编程的进入系统介面,找到那个径补偿也可以说是刀具补偿(X,Y,Z轴)可根据实际情况输入正负值。因不知道你是哪种机型所以具体步骤很难说得明白。
2.如是Z轴就更容易了,在刀具补偿设置,也可以对刀时手动抬高0.1MM3.如是电脑编程那就更容易了,直接在软件上补偿就可以了4.还有的是在加工过程中发现了NG品,要看看刀具磨损情况,单单靠调公差范围很容易造成加工 尺 寸不稳定的。再说了打个90度沉孔深了0.1MM没有多大的问题吧,
关于机床加工工件尺寸偏小和车床加工外径尺寸变化大原因的介绍到此就结束了,不知道你从中找到你需要的信息了吗 ?如果你还想了解更多这方面的信息,记得收藏关注本站。 机床加工工件尺寸偏小的介绍就聊到这里吧,感谢你花时间阅读本站内容,更多关于车床加工外径尺寸变化大原因、机床加工工件尺寸偏小的信息别忘了在本站进行查找喔。
[免责声明]本文来源于网络,不代表本站立场,如转载内容涉及版权等问题,请联系邮箱:3801085100#qq.com,#换成@即可,我们会予以删除相关文章,保证您的权利。 转载请注明出处:/jiagong/52315.html