数控机床加工现象图表-数控机床加工的基本原理
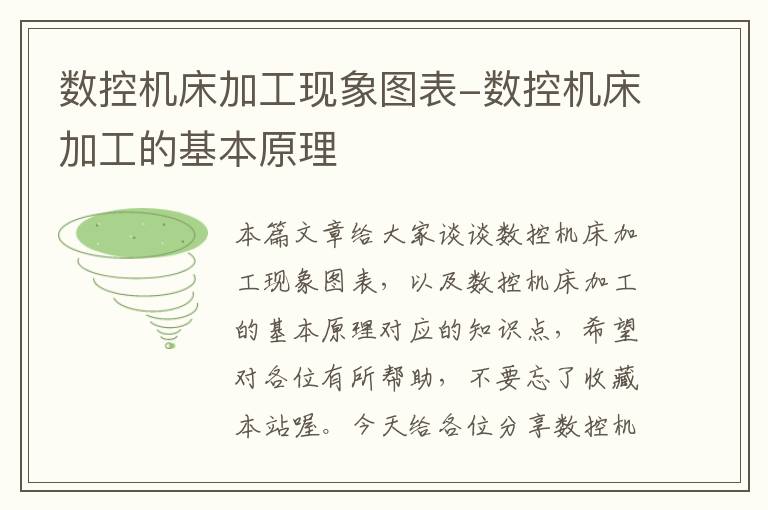
本篇文章给大家谈谈数控机床加工现象图表,以及数控机床加工的基本原理对应的知识点,希望对各位有所帮助,不要忘了收藏本站喔。 今天给各位分享数控机床加工现象图表的知识,其中也会对数控机床加工的基本原理进行解释,如果能碰巧解决你现在面临的问题,别忘了关注本站,现在开始吧!
1、求数控车床中螺纹的对照图表?
普通螺纹有大径(d、D)、中径(Dd2)、小径(Dd1)。(数字是下标,可惜这里打不出来)。
选择9齿螺纹梳刀(T03)铣削螺纹,主轴转速S=1200r/min,F=120mm/min,这种加工效率非常高,加工时间大大缩短,在大批量加工螺纹中,具有很大优势。对于不同规格的螺纹,只要选择不同的刀具即可。
度圆柱管螺纹d=D-3乘P;6:60度米制锥螺纹d=D-3乘P;注:d=螺纹小径,D=螺纹大径,P=螺距,H就是牙形高度 粗牙就是M 公称直径(也就是螺纹大径)。例如:M10,M16 细牙就是M 公称直径乘螺距。
2、数控机床震动的原因及控制方法
可能是主轴前轴承锁紧螺母松动了,你试试车外圆、切槽,如果效果也不理想,就背紧一下主轴前轴承锁紧螺母。没有专用工具的情况下可以用铜棒轻轻敲击,也不能锁得过紧,紧到空转主轴的时候手感稍重即可。
机器的因素 (1)提高数控机床自身的抗振性:可以从改善数控机床刚性,提高数控机床零件加工和装配质量方面合理保养数控机床,使其处于最佳工作状态。
原因:转速与加工件的综合主频与车床的自振频率发生了谐振。
数控车床爬行是一种故障现象. 爬行是指,机床在工进时中间用非正常的变速或停顿,这对刀具寿命和工件质量都会有影响。
位置环不良又引起输出电压不稳;速度环不良引起的振动;伺服系统可调定位器太大引起电压输出失真;传动机械装如丝杠间隙太大。这些控制环的输出参数失真或机械传动装置间隙太大都是引起振动的主要因素。
3、机床加工工件质量差的原因和解决方法是什么?
数控机床加工工件不稳定的九大原因 工件尺度精确,表面光洁度差 毛病原因:刀具刀尖受损,不尖利;机床发生共振,放置不平稳;机床有匍匐现象;加工工艺欠好。
机器精度是影响原型零件质量的重要因素。当机器精度较差,某些零件损坏或各零件间隙调整不当时,加工过程中样机就会出现各种缺陷。
以下分析是影响数控车床加工质量的主要因素,找出了问题所在,解决方法也就迎刃而解了:尺寸公差:尺寸公差是允许尺寸的变动量。
检查一下车床主轴的推理轴承间隙 2,检查进给系统各间隙。3,如果是开环系统的话,建议你被吃刀量不要太大。
装夹时,注意看清楚cnc加工工件和程式单的名称、型号是否相同,材料尺寸是否匹配,装夹高度是否够高,用卡尺卡数。
4、数控铣床如何对刀?
采用千分表对刀。该种操作方法比较麻烦,效率较低,但对刀精度较高,对被测孔的精度要求较高,该方法适用于经过铰或镗加工的孔,对于粗加工后的孔不宜采用该方法。(2)采用寻边器对刀。
数控铣床对刀的步骤如下: 选择机床上的点作为工件坐标原点,这是对刀的第一步。通常,工件坐标原点是机床上的一个已知点,它相对于机床零点的位置是已知的。 对刀时,需要选择一个刀具,将该刀具移动到工件坐标原点。
数控铣削加工的对刀 当工件以及刀具(或对刀工具)都安装好后,可按下述步骤进行对刀操作。
比如:1 拿对刀棒寻找机械坐标,然后把数值输入刀补。(前提是程序里要有刀具长度补偿指令)2 直接用刀具触碰工件表面,设为零点。
回参考点操作 采用ZERO(回参考点)方式进行回参考点的操作,建立机床坐标系。此时CRT上将显示铣刀中心(对刀参考点)在机床坐标系中的当前位置的坐标值。
5、请问一般金属材料在车床 铣床 加工中心的切削速度 和转速 还有他们之间...
在铣床上铣削工件,铣刀切削线速度V的选择,主要由刀具材料和工件材料决定。铣刀转速n(转/分钟),主要由铣刀选用切削线速度V(米/分钟)与刀具直径D(毫米)决定。
数控加工中心的切削转速和进给速度:主轴转速=1000Vc/πD 。
一般高速钢刀具线速度在9m/min~15m/min,而硬质合金刀具在60m/min~120m/min,材质硬度低可以用高的线速度,硬度高则相反。转速=1000X线速度/刀具直径,其中进给可决定你的表面光洁度。希望对你有所帮助。
通常情况下,选择适当的切削速度和进给速度是非常重要的。这可以确保刀具在加工过程中不会过度磨损或损坏,同时还能够提高加工效率和质量。
对车床转速和切削速度与进给量之间的关系,他们是互相对应的,你不紧要考虑你加工机件的材质,也要考虑你所用刀具的材质是很重要的。
关于数控机床加工现象图表和数控机床加工的基本原理的介绍到此就结束了,不知道你从中找到你需要的信息了吗 ?如果你还想了解更多这方面的信息,记得收藏关注本站。 数控机床加工现象图表的介绍就聊到这里吧,感谢你花时间阅读本站内容,更多关于数控机床加工的基本原理、数控机床加工现象图表的信息别忘了在本站进行查找喔。
[免责声明]本文来源于网络,不代表本站立场,如转载内容涉及版权等问题,请联系邮箱:3801085100#qq.com,#换成@即可,我们会予以删除相关文章,保证您的权利。 转载请注明出处:http://www.yinxishan66.cn/jiagong/7834.html