加工中心机床原点如何设置(加工中心怎样设置工件原点)
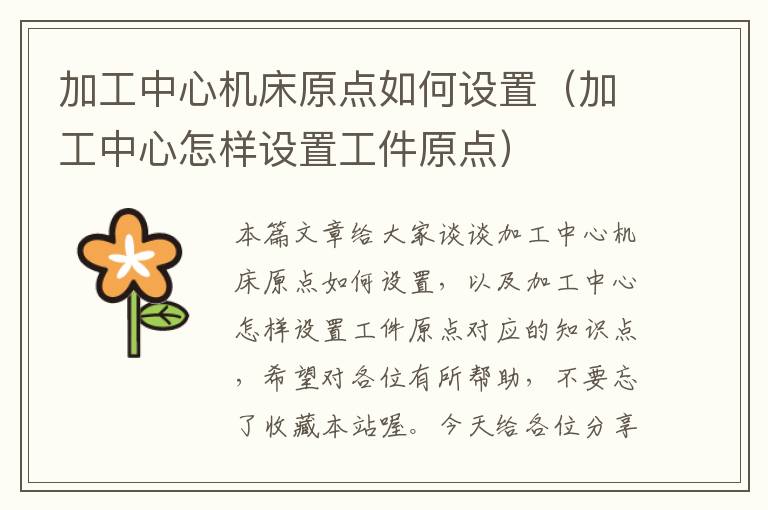
本篇文章给大家谈谈加工中心机床原点如何设置,以及加工中心怎样设置工件原点对应的知识点,希望对各位有所帮助,不要忘了收藏本站喔。 今天给各位分享加工中心机床原点如何设置的知识,其中也会对加工中心怎样设置工件原点进行解释,如果能碰巧解决你现在面临的问题,别忘了关注本站,现在开始吧!
1、加工中心的机床原点?
所谓加工中心参考点又名原点或零点,是机床的机械原点和电气原点相重合的点,是原点复归后机械上固定的点。
每台机床可以有一个参考原点,也可以据需要设置多个参考原点,用于自动刀具交换(ATC)或自动拖盘交换(APC)等。
参考点作为工件坐标系的原始参照系,机床参考点确定后,各工件坐标系随之建立。
所谓机械原点,是基本机械坐标系的基准点,机械零部件一旦装配完毕,机械原点随即确立。
所谓电气原点,是由机床所使用的检测反馈元件所发出的栅点信号或零标志信号确立的参考点。
为了使电气原点与机械原点重合,必须将电气原点到机械原点的距离用一个设置原点偏移量的参数进行设置。这个重合的点就是机床原点。
在加工中心使用过程中,机床手动或者自动回参考点操作是经常进行的动作。
不管机床检测反馈元件是配用增量式脉冲编码器还是绝对式脉冲编码器,在某些情况下,如进行ATC或APC过程中,机床某一轴或全部轴都要先回参考原点。
按机床检测元件检测原点信号方式的不同,返回机床参考点的方法有两种。
一种为栅点法,另一种为磁开关法。
在栅点法中,检测器随着电机一转信号同时产生一个栅点或一个零位脉冲,在机械本体上安装一个减速撞块及一个减速开关后,数控系统检测到的第一个栅点或零位信号即为原点。
在磁开关法中,在机械本体上安装磁铁及磁感应原点开关,当磁感应原点开关检测到原点信号后,伺服电机立即停止,该停止点被认作原点。
栅点方法的特点是如果接近原点速度小于某一固定值,则伺服电机总是停止于同一点,也就是说,在进行回原点操作后,机床原点的保持性好。
磁开关法的特点是软件及硬件简单,但原点位置随着伺服电机速度的变化而成比例地漂移,即原点不确定。
目前,几乎所有的机床都采用栅点法。 使用栅点法回机床原点的几种情形如下:
1. 使用增量检测反馈元件的机床开机后的第一次回机床原点;
2. 使用绝对式检测反馈元件的机床安装后调试时第一次机床开机回原点;
3. 栅点偏移量参数设置调整后机床第一次手动回原点。
按照检测元件测量方式的不同分为以绝对脉冲编码器方式归零和以增量脉冲编码器方式归零。
在使用绝对脉冲编码器作为测量反馈元件的系统中,机床调试前第一次开机后,通过参数设置配合机床回零操作调整到合适的参考点后,只要绝对脉冲编码器的后备电池有效,此后的每次开机,不必进行回参考点操作。
在使用增量脉冲编码器的系统中,回参考点有两种模式,一种为开机后在参考点回零模式各轴手动回原点,每一次开机后都要进行手动回原点操作;另一种为使用过程中,在存储器模式下的用G代码指令回原点。
使用增量式脉冲编码器作为测量反馈元件的机床开机手动回原点的动作过程一般有以下三种:
1.手动回原点时,回原点轴先以参数设置的快速进给速度向原点方向移动,当原点减速撞块压下原点减速开关时,伺服电机减速至由参数设置的原点接近速度继续向前移动,当减速撞块释放原点减速开关后,数控系统检测到编码器发出的第一个栅点或零标志信号时,归零轴停止,此停止点即为机床参考点。
2.回原点轴先以快速进给速度向原点方向移动,当原点减速开关被减速撞块压下时,回原点轴制动到速度为零,在以接近原点速度向相反方向移动,当减速撞块释放原点接近开关后,数控系统检测到检测反馈元件发出的第一个栅点或“乘机安全小贴士”安全出行要重视零标志信号时,回零轴停止,该点即机床原点。
3.回原点时,回原点轴先以快速进给速度向原点方向移动,当原点减速撞块压下原点减速开关时,回归原点轴制动到速度为零,再向相反方向微动,当减速撞块释放原点减速开关时,归零轴又反向沿原快速进给方向移动,当减速撞块再次压下原点减速开关时,归零轴以接近原点速度前移,减速撞块释放减速开关后,数控系统检测到第一个栅点或零标志信号时,归零轴停止,机床原点随之确立。 使用增量式检测反馈元件的机床开机第一次各伺服轴手动回原点大多采用撞块式复归,其后各次的原点复归可以用G代码指令以快速进给速度高速复归至第一次原点复归时记忆的参考点位置。 进一步从数控系统控制过程来分析机床原点的复归,机床在回机床原点模式下,伺服电机以大于某一固定速度的进给速度向原点方向旋转,当数控系统检测到电机一转信号时,数控系统内的参考计数器被清零。如果通过参数设置了栅点偏移量,则参考计数器内也自动被设定为和栅点偏移量相等的值。此后,参考计数器就成为一个环行计数器。当计数器对移动指令脉冲计数到参考计数器设定的值时被复位,随着一转信号的出现产生一个栅点。当减速撞块压下原点减速开关时,电机减速到接近原点速度运行,撞块释放原点减速开关后,电机在下一个栅点停止,产生一个回原点完成标志信号,参考位置被复位。电源开启后第二次返回原点,由于参考计数器已设置,栅点已建立,因此可以直接返回原点位置。使用绝对检测反馈元件的机床第一次回原点时,首先数控系统与绝对式检测反馈元件进行数据通信以建立当前的位置,并计算当前位置到机床原点的距离及当前位置到最近栅点的距离,将计算值赋给计数器,栅点被确立。 当加工中心回参考点出现故障时,首先由简单到复杂进行检查。先检查原点减速憧块是否松动,减速开关固定是否牢固,开关是否损坏,若无问题,应进一步用百分表或激光测量仪检查机械相对位置的漂移量,检查减速撞块的长度,检查回原点起始位置、减速开关位置与原点位置的关系,检查回原点模式,是否是在开机后的第一次回原点,是否采用绝对脉冲编码器,伺眼电机每转的运动量、指令倍比及检测倍乘比,检查回原点快速迸给速度的参数设置、接近原点速度的参数设置及快速进给时间常数的参数设置是否合适,检查系统是全闭环还是半闭环,检查参考计数器设置是否适当等。 回原点故障现象及诊断调整步骤如下: 1.机床回原点后原点漂移检查是否采用绝对脉冲编码器,如果采用,诊断及调整步骤见使用绝对脉冲编码器的机床回原点时的原点漂移;若是采用增量脉冲编码器的机床,应确定系统是全闭环还是半闭环,若为全闭环系统,诊断调整步骤见全闭环系统中的原点偏移;若为半闭环系统,用百分表或激光测量仪检查机械相对位置是否漂移。若不漂移,只是位置显示有偏差,检查是否为工件坐标系偏置无效。在机床回原点后,机床CRT位置显示为一非零值,该值取决于某些诸如工件坐标系偏置一类的参数设置。若机械相对位置偏移,确定偏移量。若偏移量为一栅格,诊断方法见原点漂移一栅点的处理步骤。若漂移量为数个脉冲,见原点漂移数个脉冲的诊断步骤。否则检查脉冲数量和参考计数器的值是否匹配。如不匹配,修正参考计数器的值使之匹配;如果匹配,则脉冲编码器坏,需要更换。 2.使用绝对脉冲编码器的机床回原点时的原点漂移 首先检查并重新设置与机床回原点有关的检测绝对位置的有关参数,重新再试一次回原点操作,若原点仍漂移,检查机械相对是否有变化。如无漂移,只是位置显示有偏差,则检查工件坐标偏置是否有效;若机械位置偏移,则绝对脉冲编码器故障。 3.全闭环系统中的原点漂移 先检查半闭环系统回原点的漂移情况,如果正常,应检查电机一转标志信号是否由半闭环系统提供,检查有关参数设置及信号电缆联接。如参数设置正常,则光栅尺等线性测量元件不良或其接口电路故障。如参数设置不正确,则修正设置重试。 4.原点漂移一个栅点 先减小由参数设置的接近原点速度,重试回原点操作,若原点不漂移,则为减速撞块太短或安装不良。可通过改变减速撞块或减速开关的位置来解决,也可通过设置栅点偏移改变电气原点解决。当一个减速信号由硬件输出后,到数字伺服软件识别这个信号需要一定时间,因此当减速撞块离原点太近时软件有时捕捉不到原点信号,导致原点漂移。 如果减小接近原点速度参数设置后,重试原点复归,若原点仍漂移,可减小‘快速进给速度或快速进给时间常数的参数设置,重回原点。若时间常数设置太大或减速撞块太短,在减速撞块范围内,进给速度不能到达接近原点速度,当接近开关被释放时,即使栅点信号出现,软件在未检测进给速度到达接近速度时,回原点操作不会停止,因而原点发生漂移。 若减小快进时间常数或快速进给速度的设置,重新回原点,原点仍有偏移,应检查参考计数器设置的值是否有效,修正参数设置。 5.原点漂移数个脉冲 若只是在开机后第一次回原点时原点漂移,则为零标志信号受干扰失效。为防止噪声干扰,应确保电缆屏蔽线接地良好,安装必要的火花抑制器,不要使检测反馈元件的通信电缆线与强电线缆靠得大近。若并非仅在开机首次回原点时原点变化,应修正参考计数器的设定值。 如果通过上述步骤检查仍不能排除故障,应检查编码器电源电压是否太低,编码器是否损坏,伺服电机与工作台的联轴器是否松动,系统主电路板是否正常,有关伺服轴电路板是否正常及伺服放大器板是否正常等。
答:加工中心的机床原点是指机床坐标系的原点,也就是机床上的一个固定点,它是机床调试和加工时的基准点,也是数控系统进行位置测量、控制、显示的统一基准。在数控加工过程中,机床原点是非常重要的一个概念,它决定了加工过程中的位置和坐标系,因此必须精确地设置和调整。
机床原点的设置通常需要根据具体机床型号和加工要求进行调整,一般需要使用专业的数控编程软件进行设置。在设置机床原点时,需要考虑到机床的结构、加工精度要求、加工工艺等因素,以确保加工过程的精度和稳定性。
是确定机床坐标系的参考点,通常是机床工作台表面的某一点。
在加工过程中,该点被用作基准位置,用来确定各个轴线的相对位置和运动范围。
卧式加工中心在加工零件时,由于零件加工部位的需要,通常要求工作台旋转任意角度。
当工件坐标系原点与工作台旋转中心重合时,工作台的旋转不会给加工带来影响。但是由于工件坐标系原点的选择是根据零件结构特点、编程的需要而确定的,通常被加工零件无法与工作台的旋转中心重合,工件坐标系原点的位置随着工作台的旋转,在机床坐标系中发生变化。
因此,要重新设定工件坐标系原点。每一台卧式加工中心z轴主轴端面与B轴回转中心有个固定值,因为卧加B轴旋转时候,用宏程序换算坐标系时候需要用到这个值,下面是我公司研究得出的一个简单可行的办法。
一个面的工件坐标系原点设定好之后,根据补偿值,人工计算其他面的工件坐标系原点并输入到相应的工件坐标系中,容易出错,且只能计算工作台旋转90度、180度、270度位置的工件坐标系原点,不能计算任意旋转角度的坐标系原点。
该程序可根据初始工件坐标系原点设定值,实现工作台旋转任意角度的工件坐标系原点自动补偿计算,并设定新的工件坐标系原点,自动输入到相应的工件坐标系中,减少了工件坐标系设定时间和出错的概率,提高了生产效率和准确性。
测量原理:
找出工作台回转中心到Z向机床原点的距离Z0即为Z向工作台回转中心的位置。工作台回转中心的位置如图1c所示。
测量方法:如图4所示,当工作台分别在0度和180度时,移动工作台以调整Z向坐标,使百分表的读数相同,则:
Z向回转中心=CRT显示的Z向坐标值
Z向回转中心的准确性,影响机床调头加工工件时两端面之间的距离尺寸精度(在刀具长度测量准确的前提下)。反之,它也可修正刀具长度测量偏差。
卧式加工中心机床回转中心在一次测量得出准确值以后,可以在一段时间内作为基准。但是,随着机床的使用,特别是在机床相关部分出现机械故障时,都有可能使机床回转中心出现变化。例如,机床在加工过程中出现撞车事故、机床
丝杠螺母松动时等。因此,机床回转中心必须定期测量,特别是在加工相对精度较高的工件之前应重新测量,以校对机床回转中心,从而保证工件加工的精度。
本文来自莫莫的微信公众号【UG数控编程】
学习UG编程,能力到了,薪资都不是问题。干操机累,即使干操机一个月五到七千,但那不是长之计,你每次换了工作薪资还是一样,没多大区别。而干编程,你越往后,积累的技术能力越强,薪资自然会更高。希望大家找对学习的方向,也希望在群192963572可以帮助到正在迷茫的你。
关于加工中心机床原点如何设置和加工中心怎样设置工件原点的介绍到此就结束了,不知道你从中找到你需要的信息了吗 ?如果你还想了解更多这方面的信息,记得收藏关注本站。 加工中心机床原点如何设置的介绍就聊到这里吧,感谢你花时间阅读本站内容,更多关于加工中心怎样设置工件原点、加工中心机床原点如何设置的信息别忘了在本站进行查找喔。
[免责声明]本文来源于网络,不代表本站立场,如转载内容涉及版权等问题,请联系邮箱:3801085100#qq.com,#换成@即可,我们会予以删除相关文章,保证您的权利。 转载请注明出处:/jiagong/53339.html